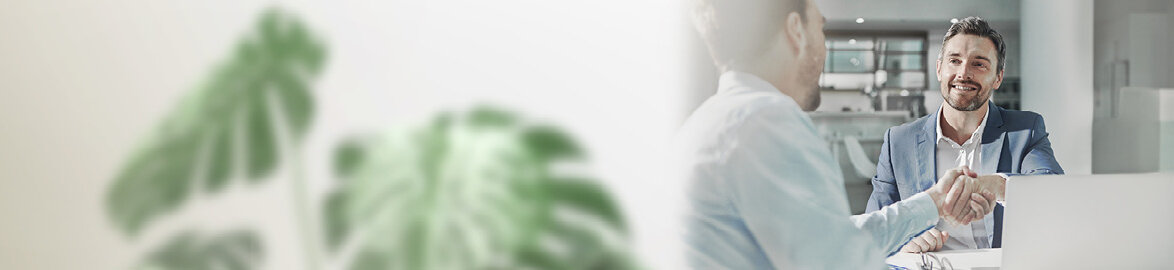
Integrated Management System at Dussmann
Quality management and quality assurance
Our quality management system is the foundation of our organisation. It provides structure and methodology, supporting all our activities through clearly identified and controlled processes, from start to finish.
This system strengthens our company’s performance by enabling early identification of risks and opportunities — a key condition for maintaining proactiveness and adaptability in complex, ever-changing environments.
It allows us to set clear objectives, measure the effectiveness of our actions, and continuously optimise the way we operate, both internally and in collaboration with our customers and partners.
At every stage of our activities — from design to execution — control and analysis are paramount. We hold ourselves to the highest standards regarding the conditions under which our products and services are delivered and used, ensuring the highest levels of customer satisfaction.
Moreover, our quality management system forms the backbone of other frameworks we deploy to address emerging challenges and key issues.
We allocate the necessary resources and implement appropriate processes to drive continuous improvement, transformation, and innovation, following a simple yet effective approach:
Collecting reliable data to deliver the right information, to the right person, at the right time — enabling informed, relevant, and effective decision-making.
Environmental management and energy efficiency
At Dussmann, our commitment to the environment is rooted in the responsible and efficient use of resources and energy.
Our environmental management system is built upon the structure of our quality management system, which serves as the common foundation for the various standards implemented at Dussmann. We continuously identify and monitor the environmental aspects of our activities, while staying alert to changes in current and upcoming legislation, as well as major trends in the field. This involves ongoing regulatory, standards, technical, and technological monitoring. Regular evaluations of our activities — and whenever necessary — allow us to define concrete actions to reduce both the direct and indirect impacts of our operations.
Our initiatives focus on:
- Defining an appropriate strategy to address environmental aspects and impacts
- Setting and achieving sustainability objectives
- Reducing consumption of resources, raw materials, and energy
- Optimising processes
- Limiting and reducing waste production
- Preventing pollution
- Implementing monitoring, control, and self-assessment systems
- Developing innovative solutions
Some practical examples include :
Improving the energy efficiency of buildings, promoting the use of renewable energy sources, oroviding training, information, and awareness programs for our staff
Occupational health and safety [management]
At Dussmann, we are deeply committed to safeguarding the physical and mental well-being of all our employees over the long term. Our goal is to foster a safe and healthy working environment, which forms the cornerstone of our approach to quality of life at work — with the ultimate ambition of one day being able to speak of true happiness at work.
Our occupational health and safety management system is built upon the same structure as our quality management system, serving as the common foundation for the various standards implemented at Dussmann.
We continuously assess the working conditions of our employees, with particular focus on the hazards inherent in our activities and the associated risks. As with our environmental management, we maintain a constant watch over applicable regulations, standards, techniques, and technologies related to our operations.
This proactive approach enables us to take relevant, timely action to prevent incidents, accidents, and occupational illnesses.
Our initiatives include:
- Defining an appropriate occupational health and safety strategy
- Setting and achieving targets for improving working conditions
- Continuously optimising our processes
- Prioritising the most effective actions in line with the 9 principles of prevention
- Promoting and ensuring comprehensive staff training
- Preventing accidents and occupational diseases
- Implementing monitoring, control, and self-assessment systems
- Improving work methods by fostering synergies between training, equipment, products, procedures, etc.
Concrete examples include:
Vaccination campaigns, access to consultations with a psychologist or psychological support units, as needed, deployment of various software tools for activity monitoring, control, and reporting